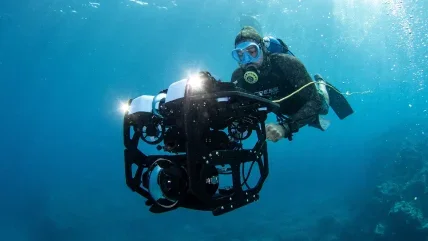
Remotely operated vehicles (ROVs), equipped with advanced sensors and dexterity, are helping to revolutionize the way maintenance and inspection tasks are carried out in hydropower plants. By venturing into the depths of turbines, dams, and other intricate infrastructure, ROVs are enhancing safety, and helping ensure efficient plant performance.
The deployment of ROVs in hydropower plants is helping to reshape the landscape of routine inspections, mitigating the risks associated with human intervention in hazardous environments. These robust machines, controlled by operators from a safe distance, can access confined spaces, navigate complex structures, and capture high-definition imagery.
Inspecting hydro dams and power plants plays a crucial role in preventing system failures and ensuring efficient energy production. By consistently monitoring submerged assets and infrastructure, both governmental bodies and private organizations can effectively anticipate maintenance needs and avert potential catastrophes.
ROVs have a diverse range of tasks they can undertake within hydropower facilities. Here are some key areas where ROVs are proving to be invaluable:
Turbine Inspections
ROVs equipped with high-definition cameras and sensors can access the submerged areas of turbine units, inspecting blades, seals, and other components for signs of damage, erosion, or debris accumulation. This enables early detection of issues that could affect turbine performance and efficiency.
Penstock and Intake Inspections
ROVs can navigate through the penstock, the pipeline that transports water to the turbine, and inspect its interior for obstructions, corrosion, or other structural problems. They can also examine intake structures for sedimentation levels, blockages, and any damage that might impede water flow.
Dam and Spillway Inspections
ROVs are employed to inspect the structural integrity of dams, inspecting areas that are difficult to reach manually. They can assess concrete conditions, identify cracks, measure sediment buildup, and check for signs of erosion or seepage. ROVs are also used to inspect spillways, ensuring their functionality and detecting any abnormalities.
Underwater Cable and Pipeline Inspections
ROVs play a crucial role in inspecting underwater power cables and pipelines. They can examine the condition of cables, identify potential faults, and locate areas that require maintenance or repair. ROVs equipped with sonar systems can detect leaks or damage in underwater pipelines, allowing for timely interventions.
Environmental Monitoring
Equipped with specialized sensors, ROVs can collect data on water quality parameters such as temperature, pH levels, dissolved oxygen, and turbidity. This monitoring helps assess the impact of hydropower operations on the surrounding environment and supports conservation efforts.
Emergency Response and Search Operations
In the event of an emergency or accident, ROVs can be deployed to perform search and rescue missions in underwater environments. They provide real-time visuals and facilitate the identification and retrieval of objects or individuals, enhancing safety and reducing human risks.
Sediment Sampling and Bathymetric Surveys
ROVs equipped with sampling mechanisms can collect sediment samples from reservoirs, aiding in the assessment of sedimentation rates and their impact on hydropower operations. Additionally, ROVs equipped with sonar systems can conduct bathymetric surveys to map underwater topography, assisting in reservoir management and planning.
Infrastructure Maintenance and Repair
ROVs can assist in performing routine maintenance tasks, such as cleaning intake screens or removing debris from underwater structures. They can also assist in repair operations by delivering tools or materials to specific locations and providing visual guidance to technicians.
Improve Inspection Planning
If inspection or maintenance further requires humans to enter the water, an ROV is an effective tool for planning dive routes or performing pre-dive checks. Having an ROV scan the area for potential dangers, identify the target, or even latch onto an object to provide a tether route increases the chance of a smooth mission. Alternatively, an ROV can also quickly be deployed alongside a diver to monitor their status as a method of communication with the topside team.
Keep Hydro Operations Running
Without any safety concerns related to divers, operations can usually continue as normal during an ROV inspection. Removing this operational downtime ensures a continuous flow of energy production for a more efficient plant.
High Quality Imaging
ROVs are equipped with high definition cameras and powerful LED lighting to produce clear imaging. Their live feed can be recorded directly to SD cards or external hard drives for later use. This is especially useful for long-term analysis to monitor the progression of potential issues, or for inspection contractors to provide footage to clients.
These are just a few examples of the tasks that ROVs can undertake within hydropower facilities. As technology continues to advance, ROVs are expected to take on even more complex and specialized roles, contributing to the efficient and sustainable operation of hydropower plants.
Tailrace inspection using ROV
ASI, a provider of underwater inspection and hydrographic survey services, recently provided underwater inspection and hydrographic survey services at a hydroelectric power plant in Western Canada. The primary objective of the project was to identify crucial areas of interest within the tailrace, such as scour, undermining, and sediment/debris accumulation. By employing a combination of advanced technologies and methodologies, ASI’s expert team collected essential data and compiled a detailed report on the project’s findings.
To conduct the survey, ASI utilized a traditional survey boat equipped with a survey-grade multi-beam echo sounder (MBES) system. This system allowed for a comprehensive 3D point cloud of the river bottom at the tailrace, providing precise spatial references. In addition to the boat-based survey, ASI employed a customized ROV outfitted with an MBES system, a 2D imaging sonar, and a high-definition video camera. This supplementary data collection method helped augment the point cloud data, validate the results obtained from the MBES survey, and provide detailed qualification of the observed features of interest.
The work resulted in the identification of numerous areas of interest using a combination of acoustic (sonar) and visual (video) means. All observations were meticulously recorded and included in the final report, delivering a comprehensive assessment of the tailrace’s condition to the client.
ASI’s solution not only provided the client with valuable baseline data but also offers a basis for future comparisons to understand any changes in the asset’s condition. This crucial information enables the power plant owner to proactively mitigate potential problems and optimize the overall performance of the hydro facility.