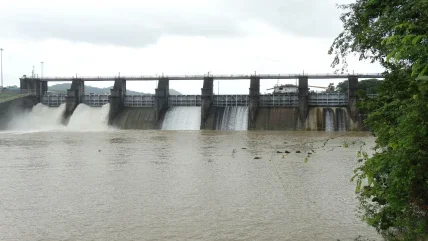
If you’re in the process of developing a new hydroelectric dam project, an important question you may be asking yourself is what kind of gate structure would serve your project best. There are a number of products available on the market that are suited to a wide range of project specifications, and below you will find details on some of the systems that are being used successfully within the industry.
Obermeyer Hydro
The Obermeyer spillway gate system is most simply described as a row of steel gate panels supported on their downstream side by inflatable air bladders. By controlling the pressure in the bladders, the pond elevation maintained by the gates can be infinitely adjusted within the system control range (full inflation to full deflation) and accurately maintained at user-selected set-points, says the company.
The spillway gate system is attached to the foundation structure by stainless steel anchor bolts (epoxy or non-shrink cement grout as design dictates). The required number of bladders are clamped over the anchor bolts and connected to the air supply pipes. When the bladder hinge flaps are fastened to the gate panels, the installation of the crest gate system is complete.
The individual steel gate panels and air bladders are fabricated in widths of five or 10ft, (1.5m or 3m for metric installations) for systems up to 6.5 ft (2m) high. Systems higher than 6.5ft (2m) use various standard width air bladders such that the height/length ration is less then approximately 1.0.
The gaps between adjacent panels are spanned by reinforced EPDM rubber webs clamped to adjacent gate panel edges. At each abutment, an EPDM rubber wiper-type seal is affixed to the gate panel edge. This seal rides up and down the stainless steel abutment plate, keeping abutment plate seepage to a minimum. For installation in cold climates the abutment plates are provided with heaters to prevent ice formation. Alternatively, rubber seals may be fixed to the abutments or piers which engage the raised gate panels.
The Obermeyer spillway gates are custom designed to conform to any existing or desired spillway cross-section with a minimum profile when in the lowered position.
The wedge-shaped profile of the gate system causes stable flow separation from the downstream edge of the gate without the vibration-inducing vortex shedding associated with simple rubber dams during overtopping. This has been developed for vibration-free operation and excellent controllability throughout a wide range of head water elevations and gate positions.
Some of the innovative features of the gates include:
• The rugged steel gate panels overhang the reinforced air bladders in all positions, and protect the air bladders from damage due to ice, logs, or other debris.
• The gates can be set at an infinite number of positions between fully raised and fully lowered, while the standard pneumatic controller provides accurate upstream pond control and discharges water appropriately to maintain upstream pond elevation through a full range of flow conditions.
• The gates use no high precision parts or bearings, which allows for easy installation and long service life, says the company.
• They use clean, dry, compressed air for actuation – no hydraulic fluid or other contaminates are used.
• The modular design of the gates has been developed to create a safe operating system. For large gate systems, each air bladder is isolated from the other by means of a check valve. If one air bladder becomes damaged, the rest of the gate system will not deflate through the damaged section.
All gates operating on the same air supply line maintain a uniform crest height. This is because any differential lowering of a gate panel relative to others on the same air supply manifold causes said gate panel to develop more contact area with its respective air bladder than other gate panels. The extra contact area produces a restoring moment which returns said gate panel to the same position as the others.
Vibration due to von Karman vortex shedding does not occur with the gates. The shape of the system when raised or partially raised causes flow separation to occur only at the downstream edge of the gate panels. This favourable condition also occurs when the system is operating in a submerged or high tail water condition.
According to the company, the gates provide very repeatable positioning relative to inflation pressure and headwater level and can be used to precisely measure the flow which they are used to control. They can also be operated continuously over a full range of gate positions, headwater elevations and tail water elevations and may be installed within siphon spillways subject to extreme water velocities.
Installation of the gates is quick and easy, claims the company. For systems up to approximately 4m high, the air bladders are secured to the spillway with a row of anchor bolts. For system heights above 4m, an embedded clamp is used to secure the gate system to the spillway. The anchor bolts may be embedded in a new spillway or may be secured in holes drilled into an existing spillway. The air supply lines which connect to each individual air bladder can be embedded or grouted into a saw slot in the spillway. Surface mounted air supply lines may also be used.
A typical installation sequence is as follows: place anchor bolts; install air supply lines; install abutment plates, if used; place air bladders over anchor bolts; secure air bladders to spillway with clamp bars; connect air supply lines to underside of air bladders; attach steel gate panels to each air bladder; attach interpanel seals; attach restraining straps if used; attach nappe breakers; adjust and grout abutment plates or install J seals; install compressor, drier and controls; and start up system.
Gates are supplied with control systems in accordance with customer requirements. Each control system includes a controlled source of compressed air and a means for controlled venting of air from the air bladders.
All automatic systems also include provision for local manual control. Each system includes an air compressor, a receiver tank, and required control valves. Most systems, especially those subject to freezing conditions, include air driers.
Obermeyer spillway gates have been installed at a number of projects across the world, including Ophua dam in New Zealand, Friant and Horseshoe dams in the US, and Rarik dam in Iceland.
hydroplus Fusegates provide an alternative solution to conventional systems (radial gates, flap gates, inflatable dams and fuseplugs for example). Fusegates provide a modular solution made up of independent units installed side by side on the dam’s spillway crest. The modules are linked by sealing joints, creating a watertight wall that increases the reservoir capacity. The size and type of fusegates varies from project to project in accordance with different needs, which the company says allows them to operate successfully in both normal and extreme conditions (significant wave action, floating debris, ice pressure, earthquakes, etc.).
Because of an inlet-well system that has progressive settings, fusegates overturn in response to very exceptional floods in a controlled, sequential approach.
Under normal conditions, fusegates increase the dam’s live storage capacity. For all floods below the first fusegate tipping level (which is set by the client, usually well above the one in 100-year flood), the fusegates act as an ungated spillway.
In the case of very exceptional floods, water rises to the level at which the first fusegate tips off the spillway sill. Water enters the inlet well and floods the base chamber, creating uplift pressure that forces the fusegate to rotate up and overturn. Fusegate tipping points are set at different levels to ensure that units overturn progressively. The sequential tipping of fusegates creates an ever-increasing opening along the spillway for the flood discharge, thereby protecting the dam from floods and possible overtopping. The progressive, accurate and carefully controlled overturning of fusegates is the mechanism that limits the effects of major floods on the downstream riverine environment, says Hydroplus
It’s important to note that fusegates only begin to overturn in the event of exceptional floods with a very low probability of occurrence. Depending on the project, the flood recurrence interval for the first Fusegate rotation could be between one in 100 and one in 10,000 years or more.
Fusegate rotation frequency can be cost-effectively adjusted in accordance with storage capacity gains and operational shortfalls related to fusegate tipping probability.
hydroplus has developed a variety of fusegate types in response to different and specific project needs. Fusegates vary in height, shape, weight, and building materials.
• Labyrinth-crested fusegates are used in situations where flood headwaters range from 30% to 140% of the height of the fusegate. The hydraulic properties associated with the labyrinth crest increase the spillway’s effectiveness.
• Straight-crested fusegates come in two standard configurations: Units designed to withstand high headwaters up to four times the height of the fusegate (these massive fusegates are
generally made of concrete and have a significant stability factor); and units designed to overturn prior to, or immediately after, being overtopped. They are generally used in conjunction with conventional gates. They increase discharge capacity under extreme flooding conditions and provide back-up in the event of malfunction by the conventional gates. As a result of their support role, these units are also called emergency fusegates.
Based on project requirements, semi-labyrinth fusegates (whose design stems from labyrinth-crested fusegates) can provide an effective alternative.
hydroplus has also developed a new system: folding fusegates. As opposed to the normal type of fusegate, folding fusegates do not overturn in the event of flooding. They stay in place and fold away, allowing discharge to flow over the crest. Post flooding, the folding fusegates are raised up in their initial position.
In July 2004, following numerous tests on scale models in the lab, a prototype was installed on the Khorobrovskaya Dam in Russia. Folding fusegates are an ideal solution for projects where the flood recurrence interval for the initial overturn is relatively short.
hydroplus says its fusegates can be used to improve:
• The storage capacity of dams
• The discharge capacity of spillways
• The flood-control characteristics of dams
• River flood management.
Fusegates may be installed during construction of new dams or on existing dams. They can be adapted to any type of dam and may be used on their own or in conjunction with conventional gates.
Fusegates have been installed with great success at a number of projects, including the Jindabyne dam in Australia, Allan dyke in France, Ghrib dam in Algeria and Otter Brook in the US.
Hydro Gate
Radial (taintor) gates from Hydro Gate are suitable for use on dams to increase reservoir capacity, and in spillways or drainage canals to maintain water elevations.
The gates have been made for two types of installations. The first, and most commonly used, is an overflow type. This gate is designed for 1ft (0.3m) of water flowing over the top of the gate when the gate is closed. Adequate safety factors prevent damage to the gate if there is a moderate, additional overflow beyond that limit for a short period of time, says the company.
The second type employs the use of a breastwall – a vertical concrete wall above the top of the gate opening that results in additional storage capacity in front of the gate. Most radial gates are raise-to-open type, a variation is the lower to open type. This requires a weir wall for mounting a seal that must make contact with the curved face plate of the gate. Silt and debris entrapment is a problem with this arrangement.
The standard radial gate face is constructed using horizontal structural members and a curved face plate. The curved steel face plate is 1/4in minimum thickness. The face plate is attached to the horizontal structural members by welding. Sufficient holes are located around the perimeter of the assembly for attaching the seals.
The horizontal face support beams are made from structural steel channels. The beams vary in size with the width of the gate and maximum head, and also vary in quantity and spacing with the height of the gate.
Welded to the end of each channel is a heavy steel gusset with holes punched to receive the side arms. These beams are normally painted, but can be hot-dip galvanised for additional corrosion protection.
Radial arms and pin plate
Radial arms are fabricated from structural steel angles, with larger and thicker angles being used as the gate height increases. Each angle acts as a column in transmitting the load from the face support channel to the pin plate. The forward or upstream end of each angle is punched with holes to match those in the gusset plate. The back end of each angle terminates at a common pin plate in a fan-like arrangement.
This steel pin plate is made thicker as the gate height, width, and head increase. A steel collar is welded to the pin plate to form a hub to receive the pin. The hub and pin are cross drilled to hold the gate pin in position. The pin is removable to facilitate installation of the gate. The entire assembly is painted, or it can be hot-dip galvanized along with the face support beams.
Bearing and pin assembly drawing
Pin bearings are a heavy cast iron housing and are bored to receive the pin. Bearings are supplied with ‘fins’ to firmly anchor them and distribute the total thrust to the concrete. Pin bearings may be aligned and supported in the forms and concrete poured around them, or a recess can be formed at the proper location in the side walls and the bearings can be grouted in place after the gate is installed. Removable coldrolled steel pins of the proper diameter are supplied to transmit the thrust on the gate to the pin bearings. The pin bearing is located high and downstream out of the water and requires no lubrication.
Seals
Side seals on both the overflow and breastwall gates are made from neoprene.
The standard side seal is a J-seal bolted to the edge of the face plate and is held in place by a steel retainer bar. The side seal is adjusted to compress against the side rubbing plate to form a watertight seal.
The bottom seal is also a J-seal that is attached to the gate by bolting. As the gate closes, its weight causes a slight deflection in the seal as it contacts the invert of the opening. This flexibility allows the bottom seal to compensate for slight irregularities in the concrete floor. However, if the floor is out of level by more than 1/8 in., the seal will not compensate for this much difference and excessive leakage will result. To minimize this possible discrepancy in construction, an adjustable sill as described in the following paragraphs is recommended.
The top seal on a breastwall-type radial gate is made by attaching a flat section of rubber to the underneath side of the breastwall. An angle attached along the top front face of the gate projects toward the breastwall and forms the other portion of the seal. As the gate is closed, the protruding leg on the angle makes contact with the rubber projecting from the breastwall and seals the space along the top of the opening. The hoist ropes pass through a slit in the seal, allowing some leakage.
To improve the operation and water-tightness of a radial gate, adjustable side rubbing plates and an adjustable bottom sill are recommended. These plates are available in stainless steel or galvanized steel.
During construction, a recess is left at the sides and bottom of the gate opening where the adjustable rubbing plates and the bottom sill are to be mounted. Anchor bolts are set in the forms and extend into the recesses. Projection of these anchors is less than the depth of the recess. When forms are stripped, the adjustable plates are installed on the projecting anchors. By use of double nuts on each anchor, the side rubbing plates and bottom sill can be properly aligned. Side rubbing plates are adjusted with the gate closed to obtain a good seal fit and compression. Side seals and side rubbing plates should be adjusted so that a slight wedge-shaped opening is formed to reduce seal drag and wear as the gate opens. The bottom sill plate must be flat across its entire width, in good contact with the bottom gate seal, and as flush as possible with the invert.
As an alignment check, the gate should operate to ensure that proper contact is being made with the rubber seals on the gate. All plates are then grouted in to complete the gate installation.
Another type of side seal available is the flat type. This is a more economical seal due to the fact that side rubbing plates are not required. It can be used for retrofitting gates in existing structures where cutting and chipping of concrete for placement of rubbing plates is not desired. The walls must be parallel, flat and perpendicular to the invert within the compliance of the flat seal. Leakage control provided by flat-type seals may not be as good as leakage control provided by J-seals and rubbing plates.
Hoist
The hoist consists of a worm gear arrangement with double drums for winding two cables simultaneously. The individual cables run from each drum to the bottom corners of the gate face.
The hoist gear box consists of a worm and worm gear totally enclosed in a cast iron housing. The housing attaches to a bracket, which in turn anchors to the top of the wall or a support beam. The drum shaft is a fabrication consisting of the drum tube spanning the opening and flanges for the rope and stub shafts at each end. One end is supported on a pillow block, the other by the gear box and bulkhead bearing. The worm is attached to a vertical shaft extending out of the gear box and is supplied with a handwheel.
Hydro Gate hoists can be motorized using an electric valve actuator attached to the top of the hoist to drive its vertical input shaft. The unit also includes an electric motor; reversing controller; push-button stations for raise, stop and lower; two indicating lights; geared limit switches; torque switches; and handwheel for emergency operation.
A hoist with an electrically operated lift mechanism can be equipped for automatic operation of the radial gate by use of logic controls to control flow and level, or to interface with other process controls.
For further details on the products described here please visit the companies websites at:
www.obermeyerhydro.com
www.hydroplus.fr
www.hydrogate.com
Details of further manufacturers of water control gates can be found on the buyers guide section of www.waterpowermagazine.com