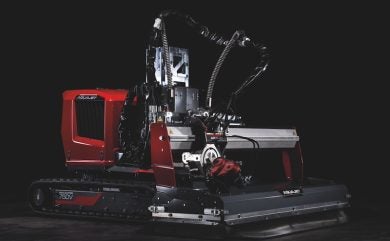
Can you provide a brief overview of Aquajet’s role and expertise in the hydropower and dams industry?
Hydrodemolition has grown in popularity for efficient concrete removal and long-lasting repairs in applications such as roads, bridges and parking garages. The technology applies to the hydropower and dam industry for the same reasons. It’s up to 25 times faster than handheld methods with low labor requirements and it offers a longer lifespan for structures. The Swedish Cement and Concrete Research Institute reports a repair life expectancy of 21-35 years with Hydrodemolition, compared to 7-12 years with mechanical chiseling.
Our customers are leveraging these advantages to successfully complete major dam projects. In British Columbia, for example, a contractor recently repaired a spillway that was cracked from years of runoff and thaw-freeze cycles.
Hydrodemolition was recommended for the project because of its ability to accelerate the repair process and increase the concrete’s life cycle. It was a complex job that needed large portions of concrete removed, but the customer used our Hydrodemolition equipment to get the job done significantly ahead of schedule.
How does Aquajet’s Aqua Cutter 750V Hydrodemolition robot work, and what makes it a valuable solution for concrete removal and surface preparation in hydropower applications?
The Aqua Cutter 750V is our newest Hydrodemolition robot that uses a high-pressure water jet up to 40,000 psi (2,758 bar) to remove layers of damaged and deteriorated concrete. The 750V introduced our patented Infinity oscillation that moves the lance in an infinity – or Figure 8 – pattern. Before this technology, Hydrodemolition has had either an oscillating lance system, which is characterized by a pendulum movement, or rotating lance system, which includes a water jet that exits at a predetermined angle. Our Infinity oscillation combines the oscillating and rotating lance movements to create the Figure 8 pattern. This allows the 750V to remove more material in a single pass, which significantly reduces shadowing and eliminates the need for any follow-up with hand lances. It also virtually eliminates pipe holes, leaving behind a superior bonding surface and increased productivity.
The versatility and efficiency of the 750V carry over to hydropower applications on spillways, dam faces, intake structures, tunnels, gates, draft tubes, tailraces and locks. We designed the 750V with exceptional vertical, horizontal and overhead reach, greatly increasing productivity for projects of all types by reaching corners and spaces that are difficult to reach. We have several accessories to help with accessibility for dam projects, such as the Aqua Spine. The Aqua Spine is a multi-modular system that adjusts from 3-19ft (1-6m) that allows contractors to reach areas inaccessible to Hydrodemolition robots. The spine can be placed on the dam spillway while the robot and pump sit elsewhere.
We’re constantly talking with customers and gathering feedback, which helps push us to develop solutions to make our equipment even more versatile. We offer accessories specific to the 750V, such as the Super Lance System, to increase our Aqua Cutters’ versatility with several different configurations. We’re putting full effort into taking the machine to the next level and ensuring customers can maximize its use.
Could you elaborate on the advantages of hydrodemolition over traditional methods, such as jackhammers, especially in terms of safety, speed, and environmental impact?
Safety, efficiency and environmental friendliness are three of the key advantages of Hydrodemolition over traditional methods. The robots are remote controlled, keeping operators out of harm’s way and virtually eliminating worker strain. Handheld methods like jackhammering produce heavy vibrations that can lead to long-term injuries, such as nerve damage and hand-arm vibration syndrome. Remote-controlled equipment also boosts productivity since it doesn’t cause operators to fatigue as quickly.
In terms of efficiency, Hydrodemolition’s ability to remove concrete significantly faster than handheld methods maximizes productivity while lowering labor costs. One operator typically controls the machine and can complete the removal task as fast or faster than multiple workers. The crew working on the dam in British Columbia conducted a test run with our Hydrodemolition equipment and it accomplished more in two days than weeks of handwork. During the project, they removed and repaired 63 cubic meters (about 2,225 cubic feet) of concrete with Hydrodemolition on cracks located at challenging 45-degree angles
Some projects and regions have strict environmental regulations, so handling the wastewater that comes with Hydrodemolition work can be a challenge. Our EcoClear water treatment system works with our full line of Hydrodemolition robots to treat wastewater generated by the process. It neutralizes water pH and greatly reduces turbidity so that it can be safely recirculated through the equipment or released back into the environment. The EcoClear moves as much as about 88 gpm or about 5,283 gallons (20 cubic meters) per hour through a series of treatment chambers that neutralizes alkaline water to a pH of 6 to 9 and reduces turbidity to only 20-25 mg particles/liter. The entire process can be monitored and controlled online with the RECO control system and enables contractors to treat wastewater in real time and maintain an environmentally sound jobsite.
How does Aquajet collaborate with clients to tailor solutions to their specific needs?
Our customers play a significant role in refining each iteration of existing technology and in developing new technology.
We constantly seek feedback to learn what works well, what can be improved and what day-to-day problems they encounter on Hydrodemolition jobs. We take that feedback and determine how to create a solution that makes their work easier and more profitable and helps advance the Hydrodemolition industry overall.
From your perspective, what are some current trends and challenges in the hydropower and dams industry, and how is Aquajet positioned to address them?
Hydropower plays an important role in providing sustainable energy but hasn’t yet gained the popularity of sources such as wind and solar.
Should hydropower become more popular in Europe and the rest of the world, dams will be more heavily relied on and efficiently repairing these dam
will be critical, which is where Hydrodemolition enters the picture. We’ll continue to manufacture innovative solutions and work closely with contractors to help problem solve and implement the most effective and efficient methods for dam rehabilitation and repair.
In summary, how would you describe Aquajet’s overall contribution to the hydropower and dams industry, and what sets it apart from other players in the market?
Aquajet offers innovative solutions to efficiently remove and repair concrete, with minimal labor. Along with that, research has shown Hydrodemolition increases the life of the repair, which is all around more economical and sustainable. Likewise, the contractors who use Aquajet products to perform Hydrodemolition services are innovators and problem solvers in their own right. Repairing these structures
is a large investment, and it is not easy work. That’s why it’s so important to bring creative solutions to achieve the best possible results safely and efficiently. That’s what Aquajet and our customers bring to the table.
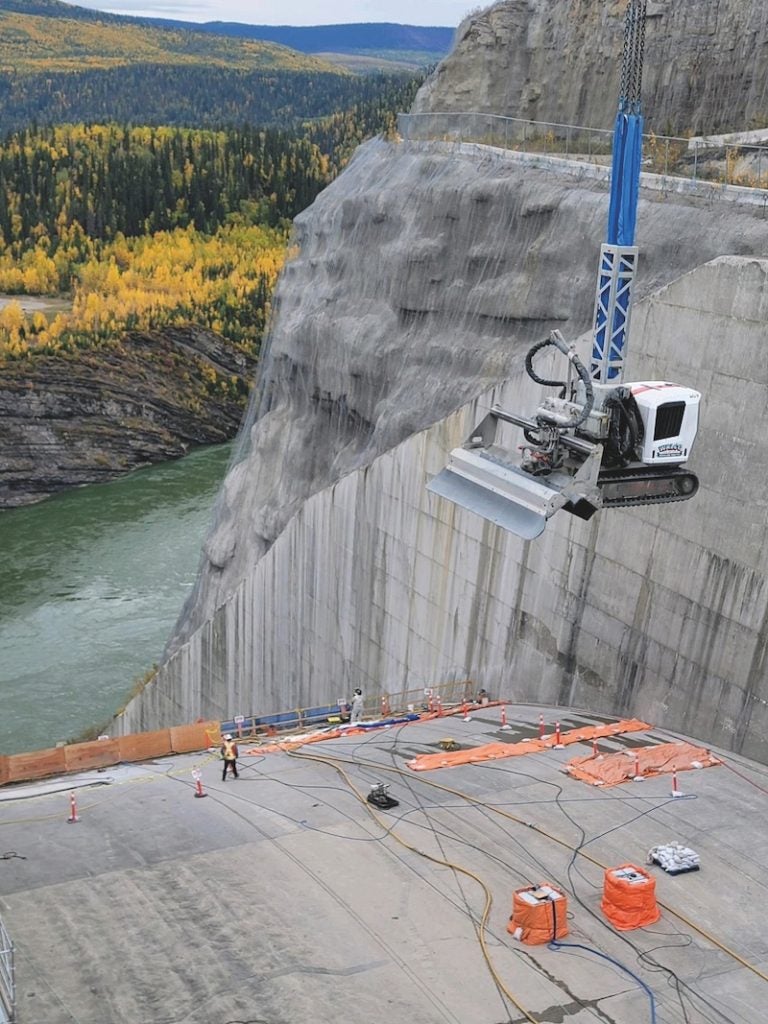