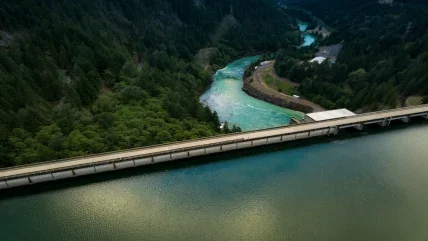
The demand for renewable energy storage systems has never been greater. While technologies, such as flywheel energy storage and compressed air energy storage are growing in popularity, pumped storage hydro, first established in the 1890s, is the largest type of grid scale energy storage system in the world.
The 2021 US Hydropower Market Report identifies how in the United States, pumped storage hydropower currently contributes 93% of grid storage. With COP26, the UN Climate Change Conference, set to be hosted later this year, the discussion of pumped hydropower storage is high on the agenda; and for good reason.
According to the International Energy Agency (IEA) Renewables 2020 Report, hydropower will account for 16% of the world’s electricity generation by 2025. For many countries, a large proportion of this will include pumped hydro storage plants. For Europe, the IEA’s Report outlines how by 2025, more than half of new hydropower capacity additions will be pumped storage power plants. The outlook is looking similar for China, with pumped storage accounting for more than half of new hydropower plants between 2023 and 2025.
The evidence is clear: investment into pumped hydro storage is on the rise, globally.
Advantages of pumped storage
In its 2020 Energy White Paper, the UK Government outlined how long-duration energy storage technologies, such as pumped hydro storage, play a crucial role in decarbonising the UK’s electricity supply. This will, crucially, help countries such as the UK and many others meet their net zero carbon emissions target by 2050, in line with the Paris Agreement.
In terms of reliability, pumped hydro storage helps to improve grid stability. Given the nature of ‘stored’ electricity, pumped hydro storage provides power whenever it is needed. In this way, it is a proven solution for meeting the reliability, capacity and timing demands of electricity consumers.
For example, according to the Environmental and Energy Study Institute’s 2019 White Paper, pumped storage hydropower is more than 80% energy efficient through a full cycle. The research also highlights how facilities can typically provide 10 hours of electricity, compared to around 6 hours for lithium-ion batteries.
Pumped hydro storage is also an economically beneficial solution. A 2021 Report by Imperial College London (ICL) stated that new pumped hydro projects could save the UK energy system between £44 million and £690 million a year by 2050. This is because, according to ICL, pumped hydro storage, is less expensive than other electricity storage technologies.
Don’t just maintain – improve
With such a rapid growth in renewable energy storage technology, the IEA says that: ‘To sustain this level, output from existing hydropower plants needs to be maintained; however, substantial amounts of generation will come from fleets that are ageing.’
The report identifies that by 2025, 40% of the world’s hydropower output will be from countries with fleets that are more than 40 years old. It highlights how this is ‘…the age at which the first major refurbishments are undertaken to either maintain or increase performance.’
As there is such a high dependency on this type of energy storage technology, asset owners should deploy appropriate repair solutions to ensure that hydropower plant integrity isn’t simply ‘maintained’, but also significantly ‘improved’ for the long term.
Key challenge areas
One of the key application areas that is subjected to large amounts of wear is the turbine runner. As the turbine runner is used in reverse as a pump during the storage phase as well, all these pieces of equipment are subjected to twice the amount of erosion compared to a standard hydropower turbine.
Similarly, bearings, blades, shafts, valves, end covers and penstocks are also subjected to twice the amount of wear per Gigawatt of energy produced during the pumped storage process.
In addition, wicket gates, stay vanes, spiral casing and draft tubes are also key challenge areas found in pumped hydro storage plants.
If maintenance issues in these key hydropower problem areas are not rectified, this can ultimately lead to reduced efficiency and therefore, profit-loss.
Indeed, in extreme cases this can even lead to asset failures and therefore unplanned shutdowns, whereby the lengthy process of decommissioning and replacing key equipment would ensue.
If it gets to this stage, not only would this seriously limit the hydro plant’s ability to serve its primary function, but this would also seriously undermine the environmental benefits of pumped hydro storage.
One repair method that is commonly employed to address these hydropower challenge areas is welding. A traditional technique, welding is often the go-to repair solution for engineers worldwide. However, it is not without its limitations.
Welding requires extensive hot work, which in turn presents significant safety risks. All flammable substances must be cleared and the area made safe for welding to take place. In many cases, this can interrupt essential operations. In addition, replacing a damaged asset with the same material will only lead to the same problems reoccurring in the future.
A solution should be sought that not only repairs the damaged assets, but also actively improves and protects them for the long term, all while avoiding the need for hot work.
Polymeric repair solutions and protective coatings
Pumped hydro storage engineers and asset owners are employing cold-curing polymeric systems as alternative repair and protection solutions.
In order to provide erosion and corrosion protection, two-part epoxy coatings can be deployed to improve the efficiency of different types of fluid handling equipment such as turbine runners.
These types of coatings improve pump efficiency by using hydrophobic technology to repel process fluids and reduce turbulent flow. In fact, efficiency increases of up to 7% have been recorded on new equipment and up to 20% on refurbished equipment.
When compared to polished stainless steel, it was found that Belzona’s epoxy coating, Belzona 1341 (Supermentalglide), was 15 times smoother.
For areas that are particularly subjected to high levels of cavitation, such as Kaplan turbine blades, abrasion and cavitation resistant elastomers can be deployed. These two-part polyurethane resins offer an outstanding level of protection against cavitation at ultra-high velocities (up to 115 knots with no damage).
Due to their erosion-resistant properties, ceramic filled coatings provide effective protection of critical equipment, such as spiral casings. These systems facilitate a fast application process, as they can be easily applied by either brush or spray.
Bearings, shafts, valves, wicket gates and stay vanes can all be repaired and rebuilt with paste grade systems. This includes two-part repair composites that are specially designed for metal repair and resurfacing based on solvent-free epoxy resins reinforced with silicon steel alloys.
These systems can all be applied and cured at room temperature, thus bypassing the need for hot work and the drawbacks this can incur.
Invest in technology
As pumped hydro storage currently represents the overwhelming majority of on-grid electricity storage, it is imperative that asset owners invest in the appropriate technology that goes beyond simply ‘maintaining’ asset integrity, but actively ‘improves’ the equipment as well.
By implementing a rigorous repair, protection and improvement strategy, key assets can be given a new lease of life. This is thanks to the efficiency enhancing and long-term erosion and corrosion resistant properties of polymeric materials.
Ultimately, these repair and protection systems support a greener future for the planet; with pumped hydropower storage being a key energy storage solution for helping industries and countries to meet net zero carbon emission targets by 2050, if not before.