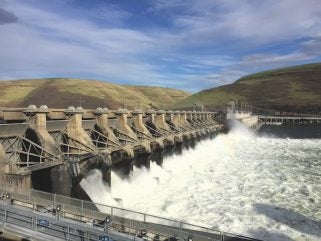
To accommodate movement and alleviate stress in concrete gravity dams, transverse expansion joints (monolith joints) are typically located every 20-30m along the axis of the dam. During construction, a barrier spanning the joint is cast into the concrete monoliths on either side: the waterstop. These joints experience frequent and recurring movements due to seasonal temperature changes, fluctuations in reservoir elevations, foundation settlements, and other factors. The cyclic movements of the joint cause the original waterstop to fatigue and eventually fail.
Failed monolith joint waterstops allow water to enter the internal rooms and galleries of the dam, and even to pass through to the downstream face. Such leakage poses numerous issues, including:
- Slip hazards
- Electrical hazards
- Downstream face icing and ice accumulation
- Excessive pumping demand
- Corrosion
- Deterioration of concrete along the joint and at joint face
- Public perception of compromised dam integrity
- Lost value of stored water through uncontrolled leakage
These issues can pose significant safety, operational, and public relations risks.
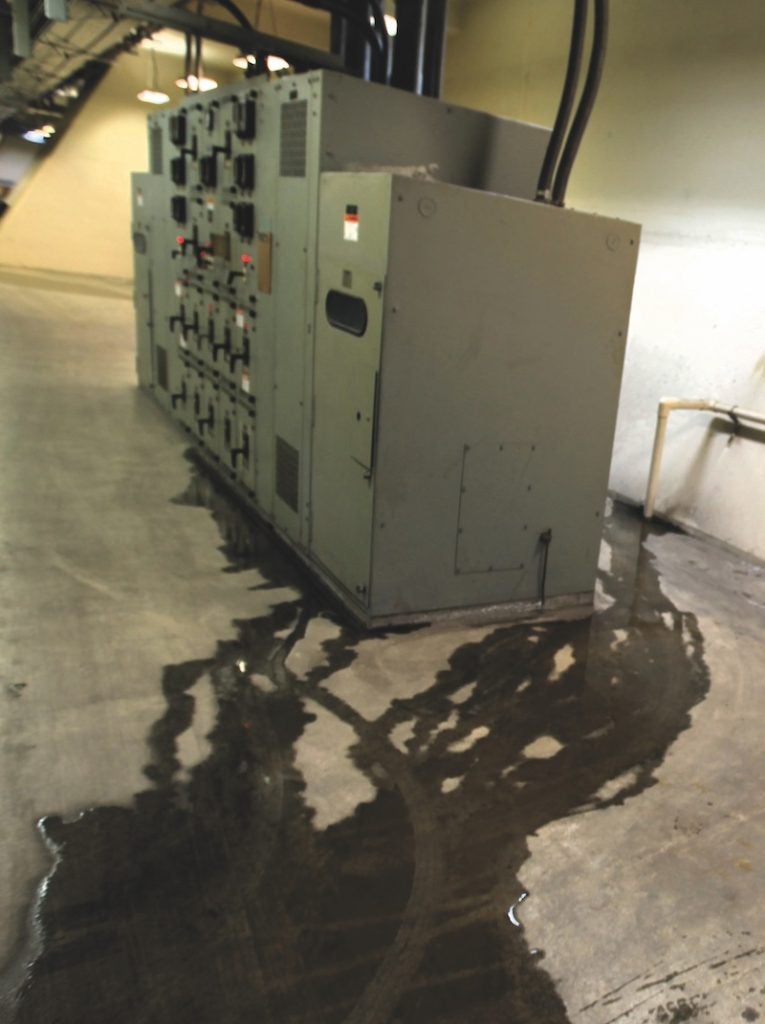
The cure
Emagineered Solutions (ESI) has developed a waterstop technology called CYLutions to help solve the unique challenge of restoring the watertight seal along monolith joints. This CYLutions process is a targeted repair from the top of dam and does not typically require marine vessels or diving. It can be performed at any time of year and installed in active leaks, under full head.
Installation of the remedial waterstop requires development of a vertical receptor hole along the full depth of the joint. This is usually accomplished by drilling a borehole, precisely centred and aligned on the joint from the top deck down to the bedrock. In some cases, an existing vertical joint drain can be re-purposed to serve as the host for the new waterstop system.
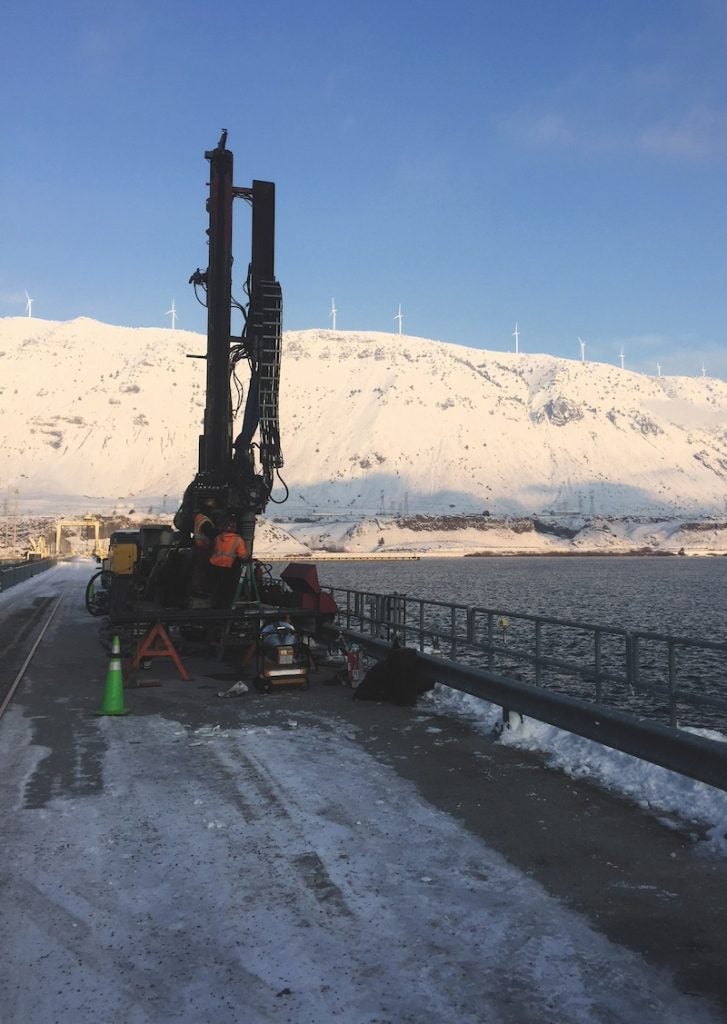
The CYLutions product is a hydrophilic polyurethane, supplied in solid rubber-like cylindrical segments, slightly smaller than the receptor hole diameter. Segment lengths can be customised to suit project constraints but are typically 1m in length. The pre-formed segments are manufactured under controlled conditions at our US facility and shipped to site, ready for installation.
Installation is performed by simply placing cylinders in the borehole by hand, one at a time, until the borehole is filled above the high water level of the reservoir. Segments swell upon immersion in water to fully fill the borehole and ultimately develop at least 325 psi (22.4 bar) of contact pressure to prevent water passage along the joint.
Once hydrated, the waterstop cylinders remain flexible and accommodate joint movements without restricting the joint. No bond is formed between the concrete and the waterstop cylinder, so the cylinders do not undergo a tension-compression cycle as the joint expands and contracts. This alleviates the fatigue experienced by other waterstop technologies that are subjected to cyclic tension and compression forces when bonded across the joint.
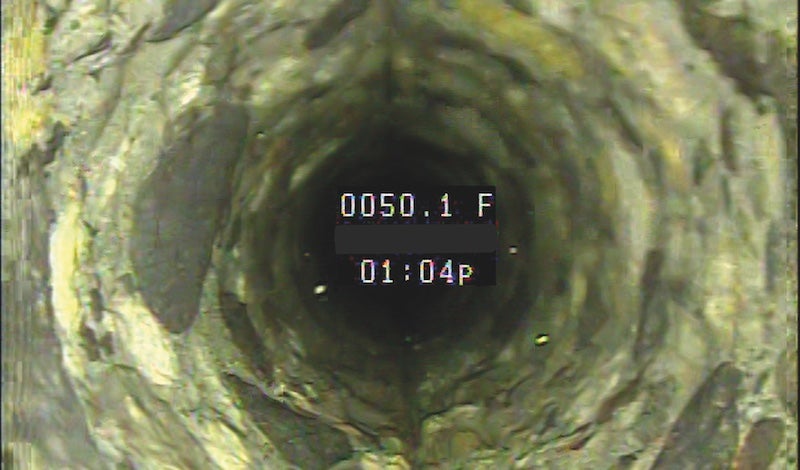
Drilled waterstops project
The John Day Lock & Dam is a straight-axis concrete gravity dam with a powerhouse consisting of 20 monoliths. Commissioned in 1971, the original waterstops had failed and leakage was entering the powerhouse galleries and operating floors along the monolith joints. Excessive flows from joint drains and through the exposed face of the joint was causing water to pool on the floors in critical areas that caused safety and maintenance issues.
A pilot project to repair three leaking joints using the CYLutions system was performed two years prior as a precursor to this project. The effectiveness of the repair on the original three locations resulted in this project to repair the remaining joints along the powerhouse monoliths.
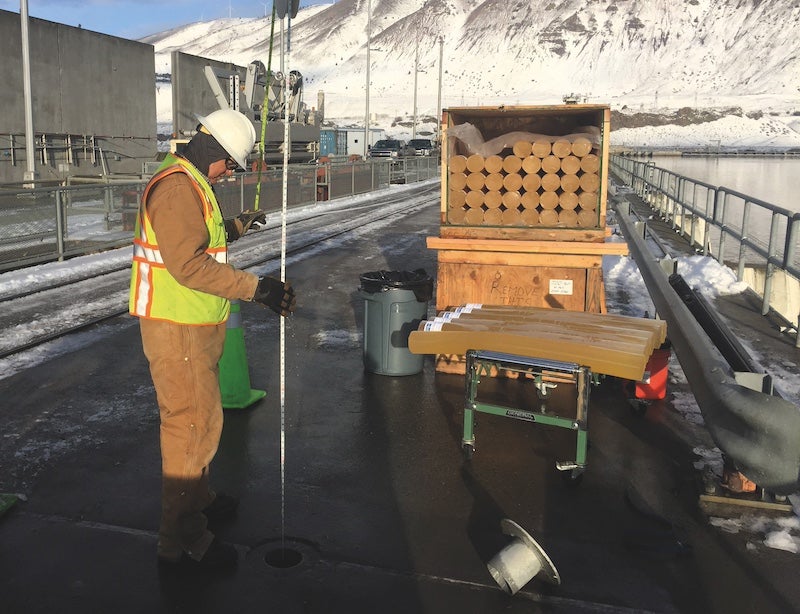
Scope of work
At each of 18 leaking monolith joints, a remedial waterstop was to be installed to mitigate the leakage into the powerhouse. A 152mm diameter borehole was drilled vertically along each joint from the top deck to a depth of 1.52m into the foundation. The average borehole depth was 53.9m. Each hole was inspected for voids or honeycombing in the concrete sidewalls of the borehole that could create a potential leakage path around the new seal. Where significant defects were identified, localized repairs were made by placing a neat-cement grout via the tremie method and then re-drilled after cure to reestablish the receptor hole.
After a final video inspection, the CYLutions remedial waterstop cylinders were installed in a column within the borehole up to 1m from the intake deck. A mechanical packer was placed on top of the cylinder stack to resist uplift of the cylinders as they expand in the presence of water.
In the weeks following installation, the leakage at all joint locations was eliminated. Dye testing that was originally scoped to determine the source of leakage persisting after installation of the waterstops was cancelled, as no visible leakage remained at the joint face or from the joint drainage system at any of the
18 joints.
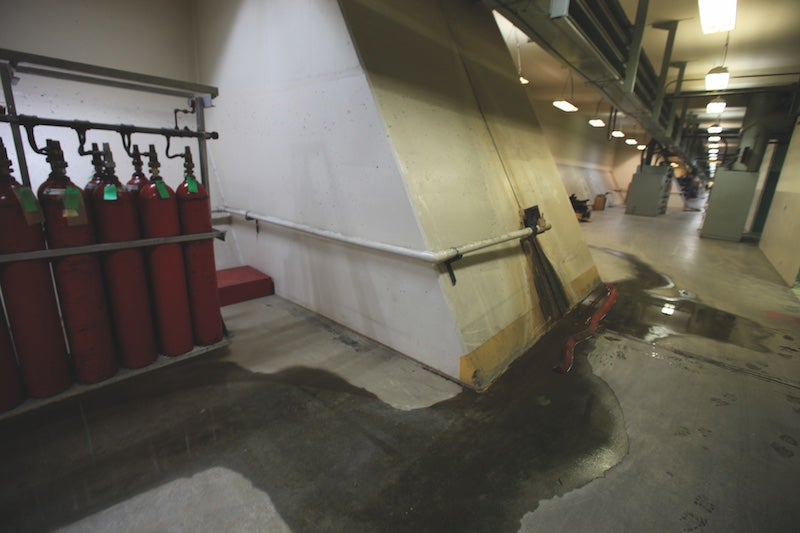
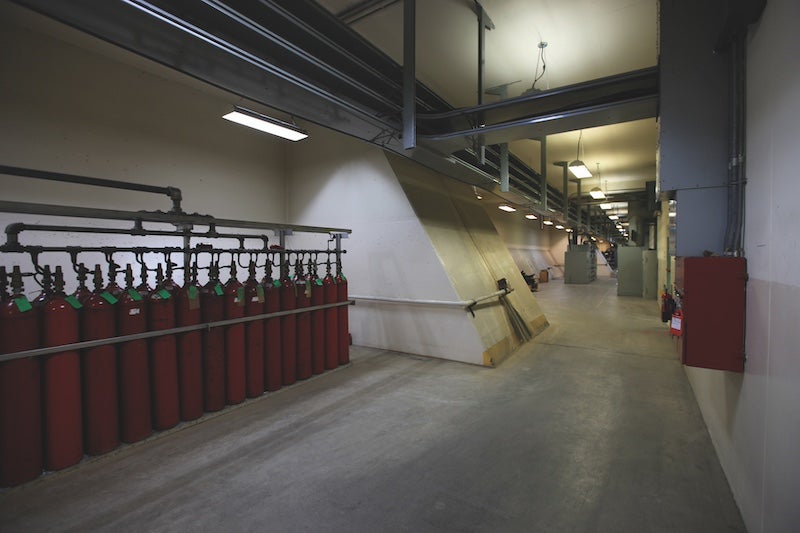
Looking forward
An opportunity exists during the design and construction phases of dams to reduce future risks and maintenance costs for the facility. Acknowledging that traditional cast-in-place waterstops will degrade due to joint movements and often prematurely fail as a result of construction deficiencies, a vertical small-diameter receptor hole (100mm – 150mm) should be formed along the joint to accommodate future installation of a remedial waterstop, such as CYLutions. This approach will reduce the cost of maintaining the joint in the future, eliminating the need to drill a precisely aligned vertical borehole after leakage develops.
Joint leakage doesn’t have to be a persistent nuisance – there is an effective long-term solution to restore the joint waterstop. The CYLutions waterstop system is suited for use worldwide in both new and existing structures, has been installed in more than 100 locations throughout North America, and has supplied remedial waterstops to projects in Scandinavia, Europe and Africa.