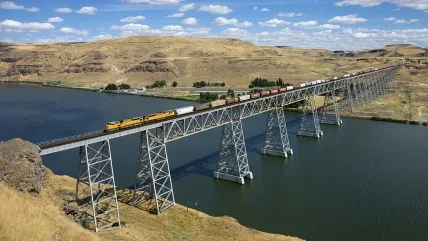
The Ice Harbor Lock and Dam on the Snake River in southeast Washington, US, just became safer for fish and more efficient at generating electricity, thanks to the installation of new turbines.
On February 17, the gantry crane at Ice Harbor hoisted 360 tons of turbine components, including an adjustable blade turbine runner, shaft, intermediate headcover and upper discharge ring insert, and carefully lowered them into their new home: the Unit 3 turbine pit in the Ice Harbor powerhouse.
This is the second of three advanced technology turbines that are scheduled to be installed at Ice Harbor. The first, a fixed blade turbine, was installed in 2018.
The turbines were designed to improve fish passage and include greaseless components and improved seal technology to reduce incidents of oil leaking into the river. On top of being better environmentally, projections indicate the new turbines are 3% to 4% more efficient at generating electricity.
The installation process for this new turbine is projected to take until the end of June, when it will go through final commissioning.
“We’re spending about four months getting everything ready, getting everything connected, checking systems individually before we actually run water through it,” Kevin Crum, project manager for the Walla Walla District, US Army Corps of Engineers (USACE), said.
Fish safety
The new turbines installed at Ice Harbor were designed to be safer for fish, reduce maintenance costs and increase power generation efficiency. The research and development started back around 1995, with the Turbine Survival Program, funded by the Bonneville Power Administration and part of the USACE Columbia River Fish Mitigation program.
The Turbine Survival Program sought to assess what factors lead to the injury of fish passing through a turbine unit, with the goal of developing operational and design improvements for turbines that would improve fish passage.
To collect data, studies were conducted using Sensor Fish developed by Pacific Northwest National Laboratory (PNNL). Sensor Fish are small autonomous devices filled with sensors that, when released through a turbine unit, can measure the physical stressors that fish may experience while passing through the unit. Engineers used these devices to study factors like the rapid decreases in pressure within the turbine environment and the likelihood of a fish being struck by a runner blade.
Other studies were done using juvenile salmonids with balloons attached. For testing, these balloon-tagged fish were released into the turbine intake. Then, after they had passed the dam, the balloons inflated, bringing the fish to the surface of the river where they were picked up and examined by researchers in a boat.
Using the data collected from these and other studies, engineers were able to design new turbines that would be safer for fish.
“Probably one of the major components that came out of the Turbine Survival Program were the models, the physical hydraulic models we used to evaluate and actually observe what the flow looks like as it passes through the turbines,” Martin Ahmann, hydraulic engineer for the Walla Walla District, and the technical lead for the turbine replacement project, said. “We also developed a method of using small, neutrally-buoyant plastic beads that we can release into the model turbine. Then, using the high-speed digital cameras, we can see how those beads interact with the components of the turbines … we can see how a fish might interact with these components by observing these neutrally buoyant particles as they pass through.”
Once developed, a new turbine design is put though vigorous rounds of testing to determine if it meets operational and fish passage parameters. Testing is performed on a 1 to 25 scale model of the turbine, constructed specifically for testing purposes. One round of testing is done by the turbine manufacturer, in Ice Harbor’s case, Voith Hydro, who checks to see if the turbine operates well from a power generation standpoint. Next, the model is shipped to Vicksburg Mississippi, where the USACE Engineering Research and Development Center (ERDC), conducts their own round of testing to see how the turbine operates from a fish passage standpoint.
Once testing is done, “we assess all the data we have, we look for the weaknesses and the strengths and we try to make improvements. Then we follow up with a new design iteration,” Ahmann said.
A turbine design can go through four or five design iterations before it is approved to be built full-scale and installed. After installation and commissioning, more testing is done to make sure the turbine meets expectations. For the fixed blade turbine, field tests indicated significant hydraulic improvements to the flow conditions, and biological testing using balloon tagged fish in October 2019 resulted in a 98.25% direct survival rate.
“It’s quite a team effort to go from a concept to having one installed like we’re seeing out at Ice Harbor,” Ahmann said.
Research for the turbine designs involved numerous federal agencies and organizations in the industry, from PNNL, to ERDC, to the Hydroelectric Design Center (HDC), USACE’s National Center for Expertise for hydroelectric and large pumping plant engineering services. Voith Hydro, in collaboration with the Corps of Engineers, developed and manufactured the designs for the Ice Harbor turbines. The effort also involved the Bonneville Power Administration’s economic expertise, and NOAA Fisheries’ knowledge of anadromous fish biology. And all of this is in addition to biologists, engineers, construction teams and contracting experts within both the Walla Walla and Portland districts of USACE.
Decades of research, development and collaboration have gone into the design of the new turbines.
“Ice Harbor and the other three other dams on the lower Snake River provide low-cost, carbon-free energy to the Pacific Northwest, and they played a major role in keeping the lights on during the winter storms of February 2021 and the heat dome event we experienced last June,” said Bill Leady, acting vice president for Generation and Asset Management at the Bonneville Power Administration. “Modernizing the equipment will benefit fish and Pacific Northwest residents well into the future.”
The history of the turbines
Ice Harbor Lock and Dam, located on the lower Snake River near Pasco, Washington, was the first of the lower Snake River dams to be constructed. The first three of its hydro-turbine units were brought online in 1961, with three additional units coming online in 1976.
In 2010, the Walla Walla District awarded a contract to Voith Hydro to design and supply one fixed blade turbine and two adjustable blade turbines at Ice Harbor. In 2016, a contract was awarded to Voith Hydro to install the three new turbines.
The first of the three new turbines, a fixed blade, was installed in the Ice Harbor powerhouse on June 8, 2018. This turbine runner was the first of its kind, designed by USACE personnel and Voith Hydro for power efficiency and to optimize the safety of fish navigating through Snake River dams.
Meanwhile in 2018, the Walla Walla District awarded a $321.3 million contract to Alstom Renewable US LLC, a General Electric Company, to design, manufacture and install 14 turbines at the McNary Lock and Dam, near Umatilla, Oregon. The 14 main unit turbines have been in operation for more than 62 years. They are projected to continue to operate on average for another seven years until the new turbines are manufactured and installed.
Looking to the future
This summer, Ice Harbor Unit 3 will be completed and functional. At that time, work on the third unit, Unit 1, will be able to begin. Unit 1 will also be an adjustable blade turbine.
Biological testing for Unit 3 is scheduled for early October. This will include Sensor Fish tests, as well as balloon-tag fish testing, where juvenile salmonids are released through the turbine unit and then evaluated for injury and survival.
And work is already well underway to design new turbines for McNary.
“We’re nearing the completion of our hydraulic design of the first adjustable blade runner of McNary. We’ll be starting that final iteration for the adjustable blade in April. So, in just a few weeks we’ll be starting the final design iteration for the adjustable blade runner. That will take us about a year, and then we’ll start the design of the fixed blade runner,” Ahmann said.
It is estimated that replacing all 14 turbines at McNary will take the next 10 to 15 years. Meanwhile, Portland District is moving forward with their own project: replacing the turbine units at John Day Lock and Dam, which was completed in 1971 and has a powerhouse with 16 turbine units.
All of these efforts are steadily reshaping and modernizing hydropower in the Pacific Northwest to be more efficient and safer for fish.