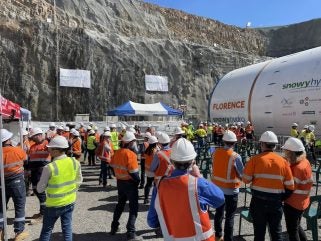
Tunnel Boring Machine (TBM) Florence has resumed excavation work for the Snowy 2.0 project after a seven-week hiatus. The machine, which is tasked with excavating the 16km headrace tunnel that connects the underground power station to the upper Tantangara reservoir, had been stalled due to exceptionally hard rock. The Snowy Delivery team used ultra-high pressure water jetting to remove the obstacle, allowing Florence to restart work on July 11. The team expects variable ground conditions ahead, which will continue to affect progress as Florence navigates the curve leading to the main tunnel alignment.
In other developments, the Snowy 2.0 team has completed significant excavation work across key areas of the project. The Talbingo intake site, where 570,000m3 of material has been removed, will manage water flow into and out of the tailrace tunnel, linking the lower Talbingo reservoir to the underground power station. At the Marica surge shaft, excavation has reached 95m. Once completed, the shaft will be 28m wide and 250m deep, serving as water storage and pressure relief for the power station.
The excavation of the gate shaft at Tantangara is also complete. This shaft will control water flow into the headrace tunnel and power station for maintenance or emergencies. The team is now advancing the excavation of the transition tunnels connecting the gate shaft to the intake.
TBM Lady Eileen Hudson has completed the 2.8km main access tunnel to the Snowy 2.0 power station and is now working on the 6km tailrace tunnel, which will connect the underground power station to the lower Talbingo reservoir. The machine has progressed approximately 3km into the tunnel. Recent modifications, including a conveyor belt extension and service upgrades, will facilitate the connection between the tailrace tunnel and the Talbingo intake excavation.
TBM Kirsten is excavating the 1.6km Inclined Pressure Shaft (IPS), connecting the underground power station to the headrace tunnel leading to the upper Tantangara reservoir. Kirsten has already completed the 2.9km emergency, cable, and ventilation tunnel and has installed 14 trial tunnel lining rings in the IPS. These rings are made of locally manufactured concrete segments designed to withstand high water pressures. The tunnelling of the IPS presents a significant engineering challenge, with the shaft’s incline reaching a steep 47%.